بیدی که دیگر با هر بادی نمیلرزد!
هجوم ویروس تاجدار به کشورها، سرعت تغییرات در میانه انقلاب صنعتی چهارم را به طور چشمگیری بالا برد. بحران کووید 19 با وجود تمام مشکلات، تجربههای ارزشمندی برای زنجیره تولید و بازار داشت. چنانچه با تکیه بر آموزههای این مهمان ناخوانده، از این پس زنجیرههای تامین قادر به تحمل هر طوفان دیگری خواهند بود.
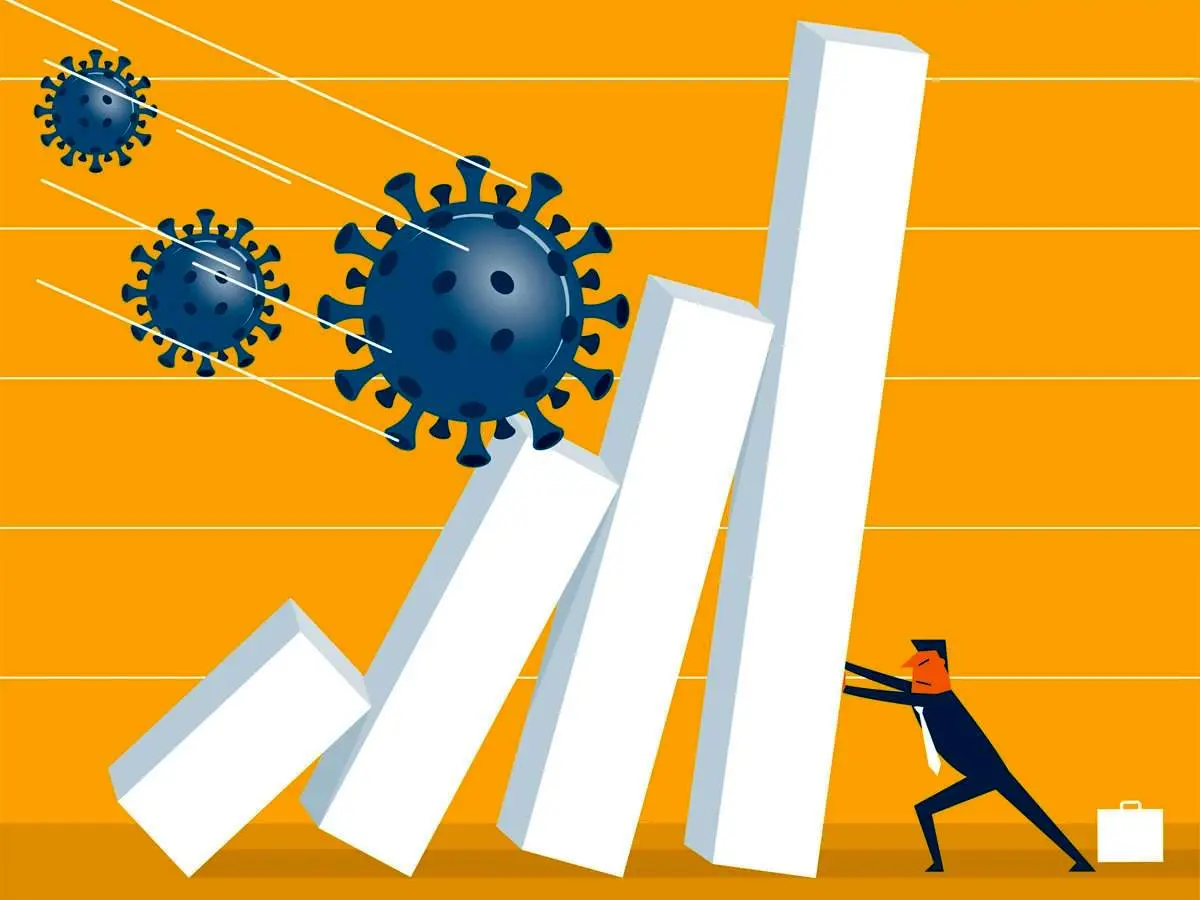
کاهش جهانی تولید از نخستین و گستردهترین آثار منفی شیوع کرونا بود که بر اقتصاد جهان تحمیل شد. چالشهای تولید در کنار محدودیتهای بازار چین و کشورهای صنعتی به عنوان مهمترین کشورهای «زنجیره تامین جهان»، تقاضای نهایی کالاها و خدمات را کاهش داد و منجر به افول ارزش سهام در بیشتر کشورهای جهان شد. این فرآیند با تغییر نیاز جهانی به انرژی، به سرعت برتقاضای نفت در بازارهای جهانی نیز تاثیر گذاشت.
اما این تمام ماجرا نبود، کاهش تولید منجر به کاهش درآمدهای صادراتی شد و تعدیل و تعطیلی کسبوکارها، درآمدهای مالیاتی را نیز محدود کرد. چالش کاهش درآمد همزمان با افزایش هزینههای حوزه بهداشت و درمان، فشار بالایی بر اقتصاد تحمیل میکرد.
چالش جدی زنجیره تامین
از سوی دیگر، چالش زنجیره تامین، تولید را با مشکلات تامین مواد اولیه و لجستیک مواجه کرد که به سرعت منجر به کاهش فروش و بهرهوری شد. مشکلات کسری بودجه و تامین نقدینگی، بر برنامهّهای حمایتی دولتها از کسبوکارها نیز تاثیر گذاشت و شرایط را برای این بخش اقتصاد بحرانیتر کرد.
در ادامه تجربه زنجیره تامین در 2 حوزه را میخوانید. مرور این تجربه نشان میدهد موفقیت زنجیره تامین در شرایط افزایش تقاضا به ویژه در بحرانهای جهانی، بستگی به آگاهی و چابکی مدیران و برنامهریزان این زنجیره دارد.
رد شلاق چرمی در قفسههای خالی
تصاویر قفسههای خالی فروشگاهها، یکی از تصاویری بود که در هفتههای نخست شیوع کرونا و رسانهای شدن خبر حمله ویروس تاجدار به کشورهای جهان به کرات دیده میشد. یکی از تصاویری که در شبکههای مجازی به سرعت دست به دست شد، مربوط به خرید وحشتزده، سوءاستفاده از منابع و دزدی دستمال کاغذ در فروشگاههای هنگکنگ بود. در آن ایام بسیاری از فروشگاهها محدودیتهایی در سرانه فروش کاغذ توالت، ضدعفونیکننده دست و سایر محصولات اعمال کردند و حتی برخی فروشگاهها بااستخدام نگهبانان امنیتی نظارت بر خرید مشتریان را بیشتر کردند. این تصویر تکراری یک پیام روشن برای برنامهریزان مدیران سازمانی و حکومتی داشت« رد «شلاق چرمی» در زنجیره تامین!»
اثر شلاق چرمی یا Bullwhip Effect که با عنوان «اثر فارستر» هم شناخته میشود، به این شکل تعریف میشود: «انحراف در تقاضا که به دلیل تنوع سفارشات (که خود ممکن است بزرگتر از میزان فروش باشند) به وجود میآید و در زنجیره تامین از پایین به سمت بالا حرکت میکند؛ یعنی از خردهفروش به عمدهفروش و تولیدکننده میرسد».
اما برای کاهش تاثیر شلاق چرمی بر زنجیره تامین چه باید کرد؟
خرید بیش از نیاز و هیجانی با هدف ذخیرهسازی کالا از سوی مصرفکنندگان نشان از «تقاضای کاذب» داشته که بر مشکلات اثر شلاق چرمی در بالادست زنجیره تامین میافزاید. بنابراین نخستین گام باید«توقف خرید هیجانی» باشد. اعمال رویکرد تطابق خرید متناسب با تقاضای واقعی نیز دومین راهکار پیشنهادی برای کاهش تاثیر شلاق چرمی بر زنجیره تامین است.
و در نهایت اینکه با این تجربه، از این پس زنجیره تامین قادر به تحمل هر طوفانی خواهند بود. درحقیقت بحران کرونا، دید متفاوتی به رهبران زنجیره تامین برای درک واقعی از میزان تقاضا و عوامل موثر بر آن داده است. تا آنجا که در صورت بروز بحرانی دوباره، این حلقه زنجیره بازار قادر به پیشبینی عرضه و تقاضای واقعی و اعمال برنامهریزهای پیشگیرانه را خواهند بود.
آنچه سیستم تولید تویوتا را مقاوم کرد
اختلال در زنجیره تامین یکی از پیامدهای اپیدمی کووید-۱۹ بود که تولیدکنندگان بسیاری را در سراسر جهان به سردرد انداخت. بیشترین تأثیر این اختلال در صنعت خودرو نمایان شد که به دنبال تعطیلی واحدهای تولیدی با کمبود شدید ریزتراشهها و سایر قطعات مواجه شد. بااینهمه شواهد حاکی از آن است که تویوتا در مقابل اختلالات زنجیره تأمین سالهای اخیر بهتر از سایر رقبا عمل کرد. در بررسی دلایل این موفقیت «انعطافپذیری در پذیرش اختلالات» در صدر دلایل بهبود ظرفیت تولید قرار میگیرد.
ویلی سی. شیه (Willy C. Shih) استاد عملکرد مدیریت در دانشکده تجارت هاروارد در مقالهای به تشریح تجربه نیلسن و جیمی بونینی، رئیس مرکز پشتیبانی سیستم تولید تویوتا (TSSC) پرداخته و مهمترین عامل موفقیت تویوتا در اپیدمی کرونا را تشریح کرده است.
در این مقاله میخوانید:
سیستم تولید تویوتا (انگلیسی: Toyota Production System) و بهطور خلاصه TPS، یک سیستم فنیاجتماعی است که به وسیله شرکت تویوتا توسعه داده شدهاست و شامل فلسفه مدیریتی و روشهای آن میباشد. TPS یک سیستم مدیریتی است که تولید و لجستیک مربوط به خودروسازی، شامل روابط متقابل با تامین کنندگان و مشتریها را سازماندهی میکند. این سیستم پیشدرآمد اصلی «تولید ناب» عمومی است که بین سالهای ۱۹۴۸ تا ۱۹۷۵ توسعه یافت و به شکل امروزی رسید.
بنیان سیستم تولید تویوتا، حذف کامل هرگونه اتلاف هزینه،زمان، انرژی و ماشینآلات است تا بهترین نتیجه ممکن حاصل شود. کیشیرو از مدیران تویوتا شرایط ایدهآل برای تولید را وقتی میدانست که هماهنگی بین کارکرد نیروی سختافزار و نرمافزار (ماشینآلات و نیروی انسانی) به تولید با ارزشافزوده و بدون هیچگونه اتلافی بیانجامد.
تایچی اونو، از مدیران پیشتاز سیستم تولید تویوتا در دهه ۱۹۵۰، بر این باور بود که «بزرگترین مشکل وقتی است که هیچگونه مشکلی وجود نداشته باشد.»
او به طور مستمر به کارکنان میگفت: به هر موضوعی که برخورد میکنید، 5 بار بپرسید «چرا؟» و با یک مثال به تشریح موضوع پرداخته و میگوید: وقتی یک روبات جوشکاری وسط کار متوقف میشود و با این پنج پرسش، ریشه مشکل به دست میآید.
چرا روبات متوقف شد؟ زیرا مدار آن بیش از حد بار کشید و فیوز سوخت.
چرا مدار بیش از حد بار کشید؟ زیرا یاتاقانها به خوبی روانکاری نشده بودند.
چرا یاتاقانها خوب روانکاری نشده بودند؟ زیرا گردش پمپ روغن ناقص صورت میگیرد.
چرا گردش روغن به خوبی صورت نمیگیرد؟ زیرا خروجی آن با آشغالهای فلزی مسدود شده است.
چرا خروجی آن مسدود شده است؟ زیرا فیلتری روی پمپ وجود ندارد.
اونو معتقد بود کشف علت ریشهای مشکلات، خود عامل و کلید حل مشکلات بعدی است. بنابراین هرچند که دادهها در تولید مهم است، اما واقعیت، مهمتر است. پس باید عمیق نگاه کرد و به ریشه رسید. از سوی دیگر در روشهای تولید تویوتا سه اصل رعایت میشود که به ترتیب تولید بهنگام، «کانبان» و «جیدوکا» است.
تولید بهنگام روشی است که در آن هر قطعه، درست هنگام نیاز، تولید میشود و ذخیرهای در انبار وجود ندارد. بنابراین روش و حجم تولید با طرح سوالهای زیر تعیین میشود:
تولید چه چیزی نیاز است؟ چه وقت نیاز است؟ چه مقدار نیاز است؟ به این ترتیب میتوان از هرگونه اتلافی جلوگیری کرد و بهرهوری را افزایش داد. از سوی دیگر با صفر کردن موجودی انبار، هزینههای نگهداری کالا در انبار حذف میشود. لازمه این کار ارتباط بسیار قوی با تامینکنندگان قطعات و مدیریت صحیح زنجیره تامین است.
آموزههای مهمان ناخوانده
در نهایت این مهمان ناخوانده علاوه بر اهمیت برنامهریزی در شرایط بحرانی، ضرورت بازنگری در زنجیره تامین را برای شرکتها نمایان ساخت. برنامهریزی منابع، تنوع تامینکنندگان، ردیابی و کنترل موجودی، ایجاد روابط استراتژیک با تامینکنندگان و استفاده از تکنولوژیهای جدید، اقداماتی هستند که میتوان برای بهبود قابلیت زنجیره تامین بکار بست.
بحران کرونا نشان داد که همکاری و همبستگی بین سازمانها، صنایع و کشورها امری بسیار حیاتی است و به شرکتها آموخت که باید زمان و انرژی لازم را صرف برنامهریزی و آمادگی برای بحرانهای آینده کنند. ارزیابی ریسکها، تدوین طرحهای بحرانی، آزمایش سناریوها، آموزش کارکنان و آمادگی روانی و روحیه مثبت، عواملی هستند که به شرکتها در مقابله با بحرانها و حفظ پایداری کمک خواهند کرد.
متن کامل این مقالات و مجموعه ای از مطالب دیگر درباره استراتژی بقای کسبوکار را در ماهنامه سرانه بخوانید.